How to Track Your Refrigerated Last-Mile Delivery with Peace of Mind
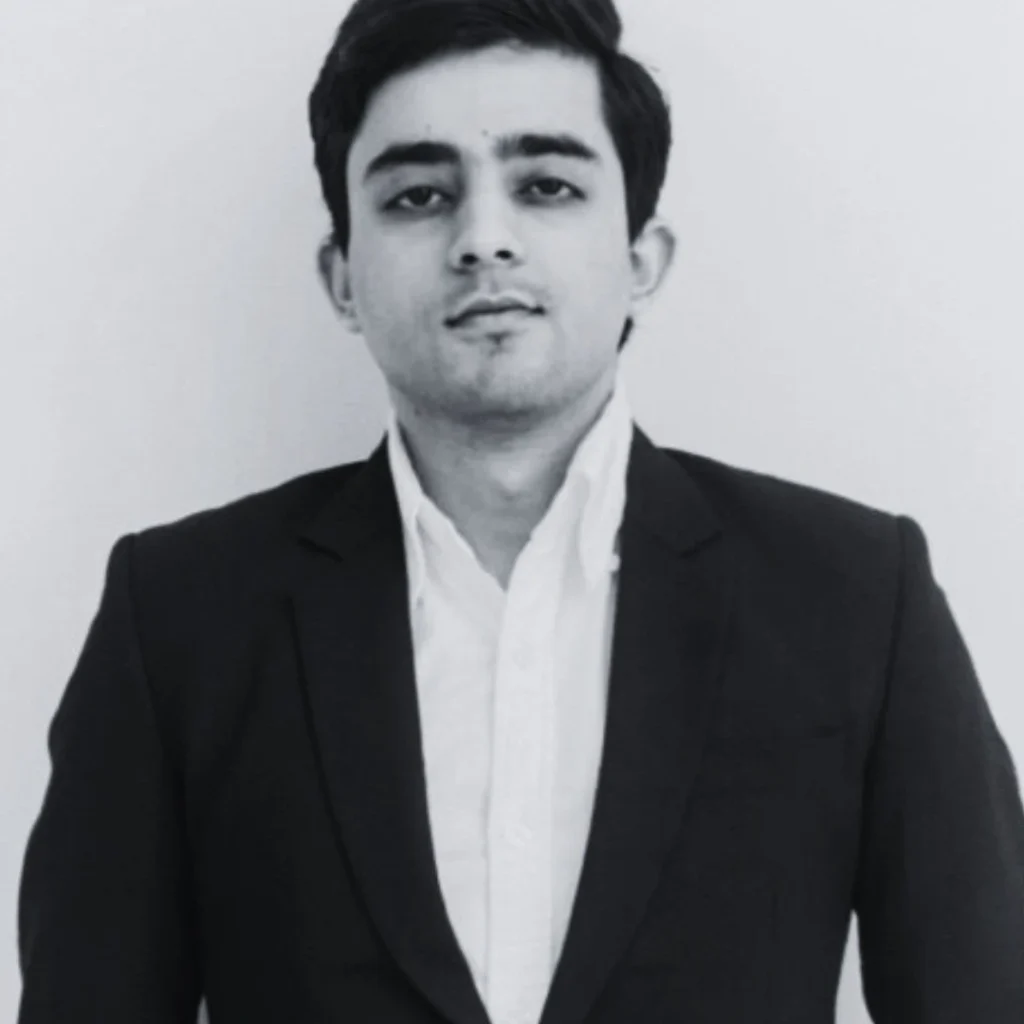
Akshay Sharma
CEO's Office @ZEVO
Ever stare longingly out the window, phone clutched in hand, waiting for that perfect scoop of ice cream after a long day? The delivery info is as helpful as a melted popsicle.
“Out for delivery” it says, but where? Stuck in traffic, perhaps? Baking under the summer sun? The thought of a puddle of chocolate sludge instead of your promised pint sends shivers down your spine (almost as bad as the heat!).
On the flip side, businesses offering frozen food deliveries share your anxieties. The “last mile” – that crucial leg from their warehouse to your door – can be a frozen food fiasco if temperatures aren’t meticulously controlled.
Imagine dealing with customer complaints about ruined frozen dinners or medication rendered ineffective due to improper temperature control. Maintaining a specific temperature range, typically between 2°C and 8°C, is vital for both food safety and efficacy. But how can businesses ensure your deliveries stay perfectly chilled until they reach their destination?
Thankfully, there’s a new hero in town for both customers and businesses: real-time tracking with temperature monitoring for refrigerated deliveries.
Ensuring Safe Deliveries: The Role of Data Loggers
So, how does this real-time temperature tracking magic happen? It all comes down to tiny tech heroes called data loggers. These little gadgets are tucked inside the delivery vehicles or containers, silently monitoring and transmitting crucial information about the temperature of your precious cargo. Think of them as temperature spies, sending back updates on the conditions inside the delivery mobile.
But how exactly do these data loggers work their magic? Here’s a breakdown:
- Sensing the Heat: Data loggers are equipped with highly sensitive temperature sensors. These sensors constantly measure the temperature inside the delivery vehicle or container.
- Data Recording: The data logger doesn’t just measure the temperature, it also records it! This creates a continuous record of the temperature throughout the entire delivery journey.
- Setting the Limits: You can program the data logger with specific temperature thresholds. If the temperature inside the container strays outside this safe zone (like exceeding the 2°C to 8°C range for medications), the data logger can trigger an alert.
- Going Wireless (Optional): Some data loggers have built-in wireless capabilities. This allows them to transmit the temperature data in real-time to a central server or even your smartphone. With real-time updates, you can see the current temperature of your delivery at any given moment.
- Downloadable Data (Optional): Even data loggers without real-time transmission capabilities are valuable. They can store the temperature data internally, allowing businesses to download it upon delivery. This provides a historical record of the temperature throughout the journey, which can be helpful for quality control and identifying any potential temperature excursions.
Here’s where things get interesting – there’s actually a variety of data loggers used for refrigerated deliveries, each with its own strengths:
Now, let’s talk about how this data gets to you. There are two main types of data loggers based on how they transmit information:
As you can see, the world of data loggers is all about finding the right tool for the job. By using the appropriate type, delivery companies can ensure your groceries, frozen food, and even medications stay fresh and safe throughout their journey!
Temperature Control: Keeping Products Fresh or Frozen
Now that we’ve unveiled the data logger, the unsung hero of real-time temperature tracking, let’s delve into the science behind keeping your deliveries fresh or frozen. This concept, known as the cold chain, ensures products maintain specific temperature ranges throughout the entire delivery journey, from warehouse to doorstep. Maintaining proper temperature control is critical for several reasons:
- Life-Saving Drugs: Certain medications, particularly vaccines and biologics, can lose their efficacy or even become harmful if exposed to excessive heat or cold. Data loggers with external probes become crucial here, ensuring precise temperature monitoring in specific locations near these sensitive items. For instance, most vaccines require a constant temperature range between 2°C and 8°C for optimal effectiveness.
- Frozen Food Quality: Fluctuations in temperature can wreak havoc on frozen food. Once thawed and refrozen, these products are susceptible to spoilage, loss of texture, and even flavor changes. Maintaining a constant frozen temperature, typically around -18°C, throughout the delivery process ensures the quality and safety of your favorite ice cream or frozen veggies.
- Fresh Produce Safety and Quality: Fresh fruits, vegetables, and dairy products have ideal temperature ranges for optimal quality and to prevent the growth of harmful bacteria. For example, most fruits and vegetables thrive between 7°C and 13°C, while dairy products generally require cooler temperatures between 1°C and 4°C. Real-time temperature monitoring with data loggers allows businesses to identify any potential temperature excursions during delivery, ensuring the safety and freshness of these perishable groceries.
By understanding the critical role of temperature control and leveraging the data provided by loggers, businesses can optimize their cold chain management. This not only ensures product quality and safety for the consumer but also minimizes spoilage and product waste, leading to a more sustainable and cost-effective delivery system. In the next section, we’ll explore how real-time tracking with temperature monitoring benefits both businesses and customers.
Quantifying the Advantage: Benefits of Real-Time Tracking with Temperature Monitoring
Now that we’ve explored the technical aspects of data loggers and the importance of maintaining the cold chain, let’s translate this into tangible benefits for both businesses and customers.
Businesses Unlock Efficiency and Trust:
- Improved Customer Satisfaction: Real-time temperature data empowers customers. They can see for themselves that their deliveries are maintained within the proper range, reducing anxiety about spoilage or compromised efficacy. This translates to fewer inquiries and complaints for businesses, freeing up valuable resources.
- Efficient Scheduling: Imagine having a real-time map displaying not only the location of your delivery vehicles but also the temperature readings inside each one. This allows for dynamic route optimization, ensuring deliveries arrive faster and at the optimal temperature. The result? Lower fuel costs and a more streamlined delivery process.
- Increased Transparency: Building trust with customers is paramount. Real-time temperature monitoring provides documented proof that temperature-sensitive products are handled with care throughout the entire delivery journey. This transparency fosters customer loyalty and can be a valuable differentiator in a competitive market.
- Industry-Specific Advantages: Consider the example of grocery delivery. Real-time temperature tracking can ensure the integrity of medications delivered alongside groceries, maintaining both safety and efficacy. This allows businesses to expand their service offerings and cater to a wider customer base.
Customers Gain Peace of Mind and Control:
- Peace of Mind: No more pacing by the window, wondering if your medication is still potent or your groceries have become a science experiment. Real-time tracking with temperature monitoring provides a clear picture of your delivery’s status, alleviating anxiety and ensuring peace of mind.
- Efficient Scheduling: Knowing exactly when your delivery will arrive, along with the assurance of proper temperature control, allows you to plan your day accordingly. This eliminates the inconvenience of missed deliveries or the worry of perishable items sitting outside for extended periods.
- Increased Control: Some advanced tracking systems allow customers to request changes to their delivery window or provide specific instructions for drivers. This level of control empowers you to customize your delivery experience and ensure a smooth and convenient process.
Real-time tracking with temperature monitoring offers a win-win situation for both businesses and customers. Businesses gain valuable insights for optimizing their operations, while customers enjoy peace of mind and a more convenient delivery experience. In the final section, we’ll explore the future of this technology and how it could further revolutionize the last-mile delivery landscape.
Going Beyond Tracking: A Look at the Future
Real-time tracking with temperature monitoring is more than just a cool tech gimmick; it’s a crucial piece of the puzzle in the evolving world of supply chain transparency and customer experience. By offering customers a window into the delivery process and ensuring the integrity of temperature-sensitive products, this technology fosters trust and builds loyalty.
But the story doesn’t end here. The future holds exciting possibilities for even greater efficiency and innovation:
- AI-Powered Route Optimization: Imagine a world where artificial intelligence (AI) takes the wheel of delivery route planning. By integrating real-time traffic data, weather forecasts, and temperature monitoring information, AI could optimize delivery routes in real-time, ensuring faster deliveries and minimal temperature fluctuations. This could be a game-changer for perishable goods, further reducing spoilage and waste.
- Predictive Maintenance: Advanced data analysis could allow businesses to predict potential equipment failures in refrigerated vehicles. Imagine receiving an alert before a critical sensor malfunctions, allowing for preventative maintenance and avoiding disruptions to the cold chain. This proactive approach would minimize product loss and ensure a more reliable delivery experience.
- Sustainable Deliveries: Real-time data on fuel consumption and route optimization could pave the way for more sustainable delivery practices. By streamlining routes and reducing unnecessary travel, businesses can minimize their environmental footprint. This aligns perfectly with the growing focus on eco-friendly solutions and could be a valuable marketing advantage.
The future of last-mile refrigerated deliveries is bright. Real-time tracking with temperature monitoring is just the first step in a journey towards greater transparency, efficiency, and sustainability. As technology continues to evolve, we can expect even more innovative solutions that benefit both businesses and customers, ultimately creating a win-win for everyone involved in the delivery chain.
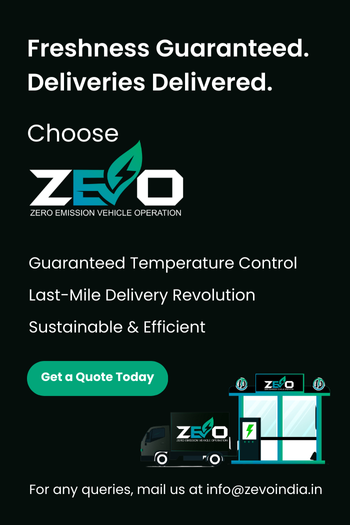
Share this Article
Subscribe to our newsletter
Be the first to receive exclusive offers and the latest news on our products and services directly in your inbox.